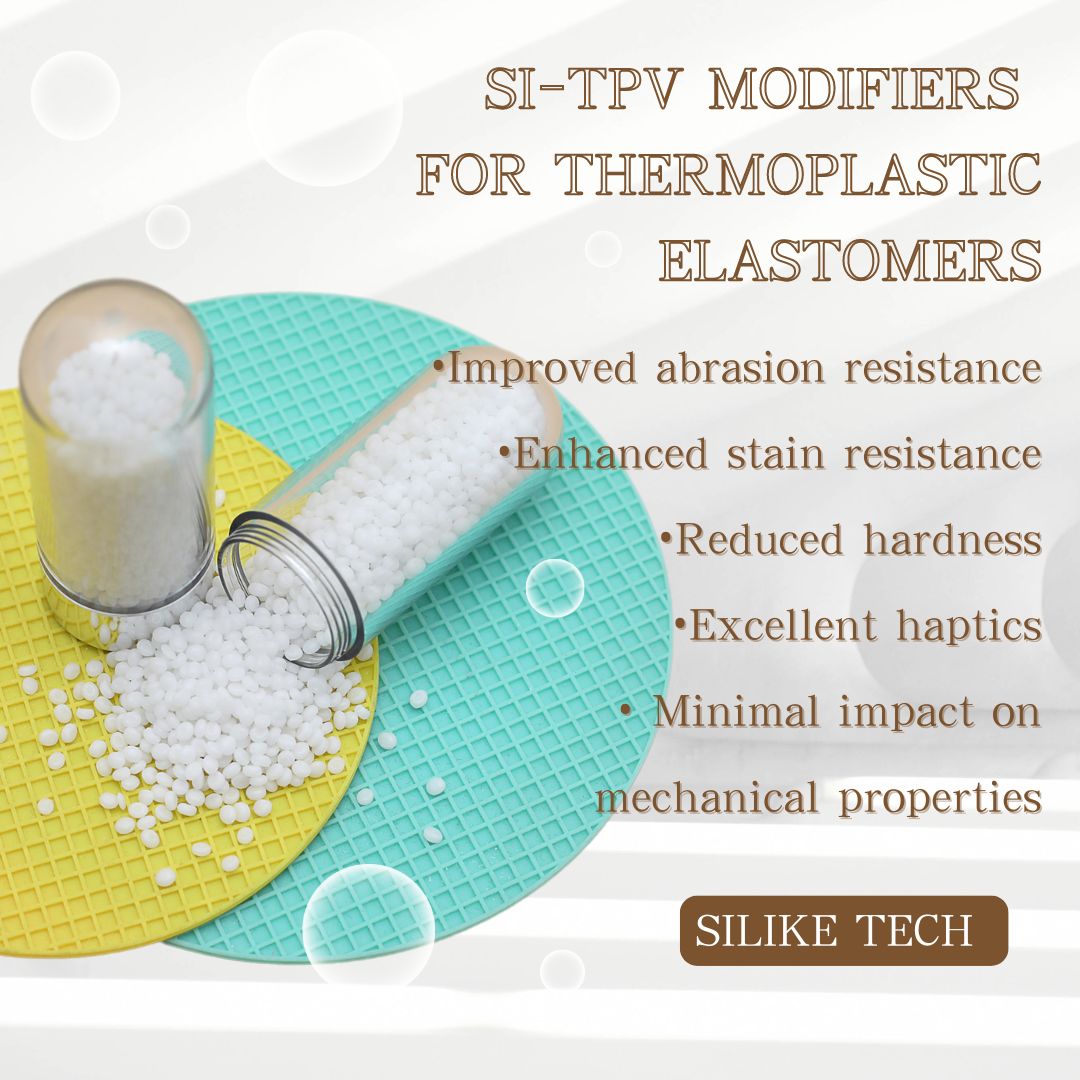
Thermoplastic elastomers (TPEs) are a versatile class of materials that combine the characteristics of both thermoplastics and elastomers, offering flexibility, resilience, and ease of processing. TPEs have become the premier choice for appliance designers and engineers seeking soft, elastomeric materials. These materials are widely used in various industries, including automotive, consumer goods, medical devices, electronics, HVAC, and other industrial applications.
Classifying TPEs
TPEs are classified by their chemical composition: Thermoplastic Olefins (TPE-O), Styrenic compounds (TPE-S), Vulcanizates (TPE-V), Thermoplastic Polyurethanes (TPE-U), Copolyesters (COPE), and Copolyamides (COPA). In many cases, TPEs like polyurethanes and copolyesters are over-engineered for their intended application when a TPE-S or TPE-V would be a more suitable and cost-effective choice.
Conventional TPEs generally consist of physical blends of rubber and thermoplastic resins. However, thermoplastic vulcanizates (TPE-Vs) differ as the rubber particles in these materials are partially or fully cross-linked to enhance performance.
TPE-Vs offer lower compression set, better chemical and abrasion resistance, and superior performance at high temperatures, making them ideal candidates for rubber replacement in seals. Conventional TPEs, on the other hand, offer greater formulation versatility, allowing them to be custom-tailored for specific applications, such as consumer products, electronics, and medical devices. These TPEs typically have higher tensile strength, better elasticity ("snappiness"), superior colorability, and are available in a broader range of hardness levels.
TPEs can also be formulated to adhere to rigid substrates like PC, ABS, HIPS, and Nylon, providing the soft-touch grips found on products like toothbrushes, power tools, and sports equipment.
Challenges with TPEs
Despite their versatility, one of the challenges with TPEs is their susceptibility to scratches and mar, which can compromise both their aesthetic appeal and functional integrity. To address this issue, manufacturers increasingly rely on specialized additives that enhance the scratch and mar resistance of TPEs.
Understanding Scratch and Mar Resistance
Before exploring specific additives, it's essential to understand the concepts of scratch and mar resistance:
- Scratch Resistance: This refers to the material's ability to withstand damage from sharp or rough objects that might cut or dig into the surface.
- Mar Resistance: Mar resistance is the material's ability to resist minor surface damage that may not penetrate deeply but can affect its appearance, such as scuffs or smudges.
Enhancing these properties in TPEs is crucial, particularly in applications where the material is exposed to constant wear and tear or where the appearance of the final product is critical.
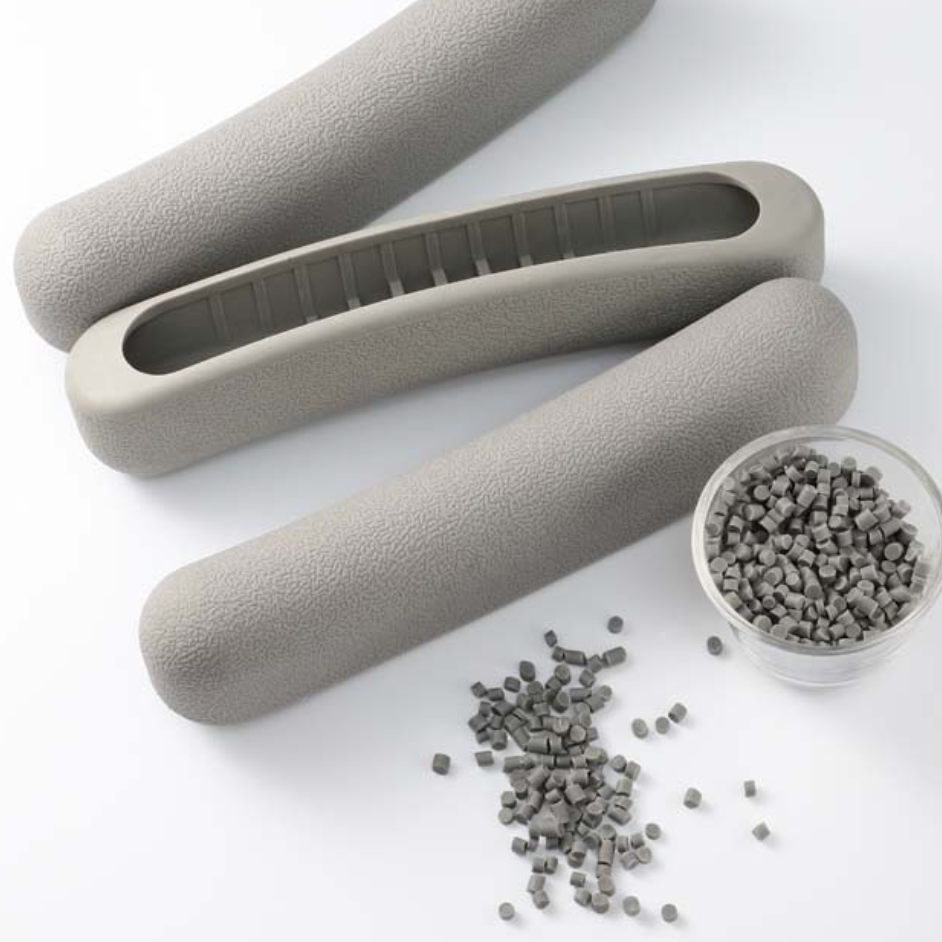
Ways to Enhance Scratch and Mar Resistance of TPE Materials
The following additives are commonly used to improve the scratch and mar resistance of TPEs:
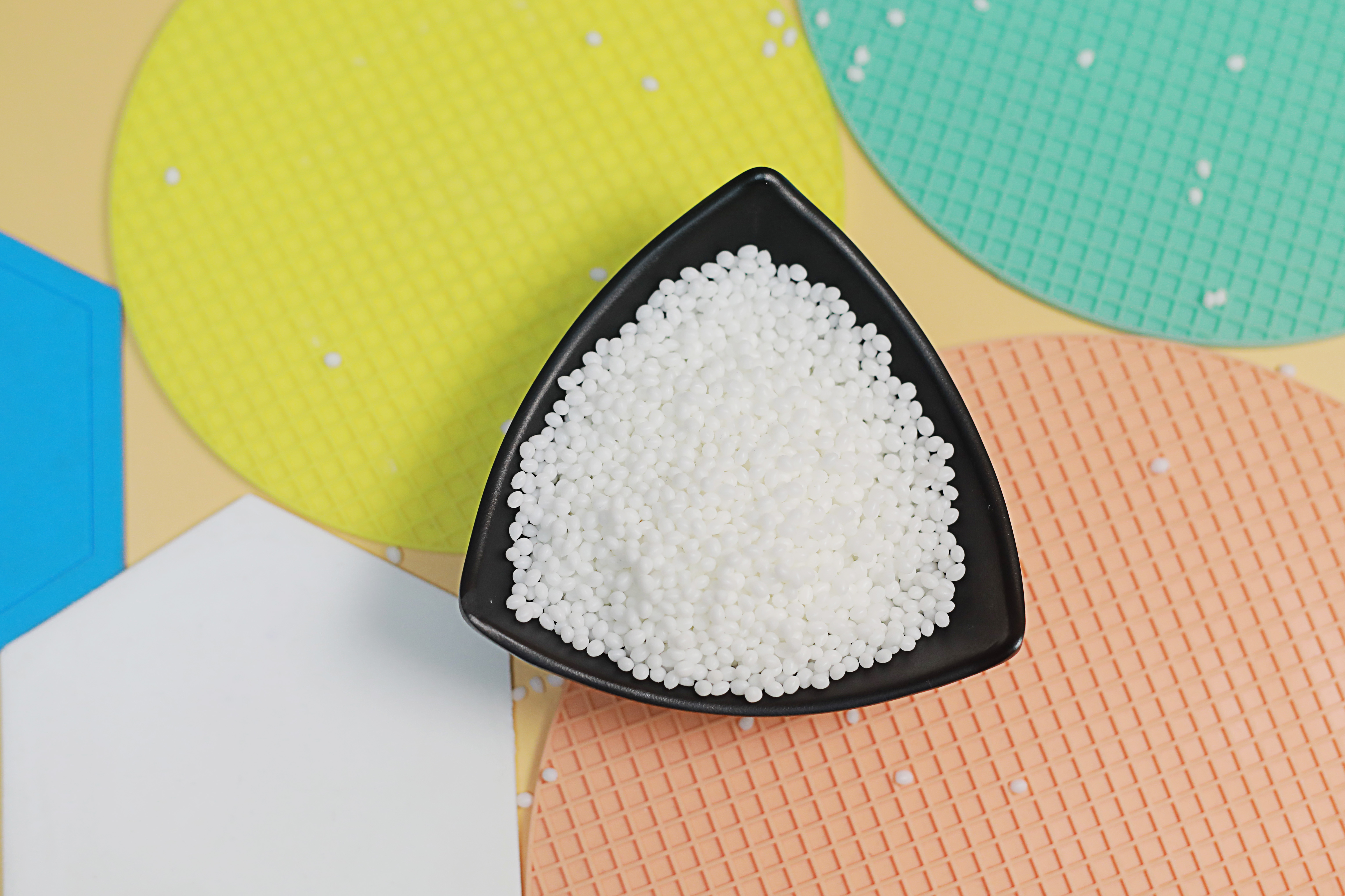
1.Silicone-Based Additives
Silicone-based additives are highly effective in enhancing the scratch and mar resistance of thermoplastic elastomers (TPEs). These additives work by forming a lubricating layer on the surface of the material, reducing friction and thereby minimizing the likelihood of scratches.
- Function: Acts as a surface lubricant, reducing friction and wear.
- Benefits: Improves scratch resistance without significantly affecting the mechanical properties or flexibility of the TPE.
Specifically, SILIKE Si-TPV, a novel silicone-based additive, can serve multiple roles, such as a Process additive for thermoplastic elastomers, Modifiers for Thermoplastic elastomers,Thermoplastic Silicone-based elastomers modifier, Thermoplastic elastomers feel modifiers. The SILIKE Si-TPV Series is a dynamic vulcanized thermoplastic silicone-based elastomer, created using specialized compatibility technology. This process disperses silicone rubber within TPO as 2-3 micron particles, resulting in materials that combine the strength, toughness, and abrasion resistance of thermoplastic elastomers with the desirable properties of silicone, such as softness, a silky feel, UV light resistance, and chemical resistance. These materials are also recyclable and reusable within traditional manufacturing processes.
When Silicone-Based Thermoplastic Elastomer (Si-TPV) is incorporated into TPEs, the benefits include:
- Improved abrasion resistance
- Enhanced stain resistance, evidenced by a smaller water contact angle
- Reduced hardness
- Minimal impact on mechanical properties with the Si-TPV series
- Excellent haptics, providing a dry, silky touch with no blooming after long-term use
2. Wax-Based Additives
Waxes are another group of additives commonly used to enhance the surface properties of TPEs. They work by migrating to the surface, creating a protective layer that reduces friction and improves resistance to scratches and marring.
- Types: Polyethylene wax, paraffin wax, and synthetic waxes are frequently used.
- Benefits: These additives are easy to incorporate into the TPE matrix and offer a cost-effective solution for improving surface durability.
3. Nanoparticles
Nanoparticles, such as silica, titanium dioxide, or alumina, can be incorporated into TPEs to enhance their scratch and mar resistance. These particles reinforce the TPE matrix, making the material harder and more resistant to surface damage.
- Function: Acts as a reinforcing filler, increasing hardness and surface toughness.
- Benefits: Nanoparticles can significantly enhance scratch resistance without compromising the elasticity or other desirable properties of TPEs.
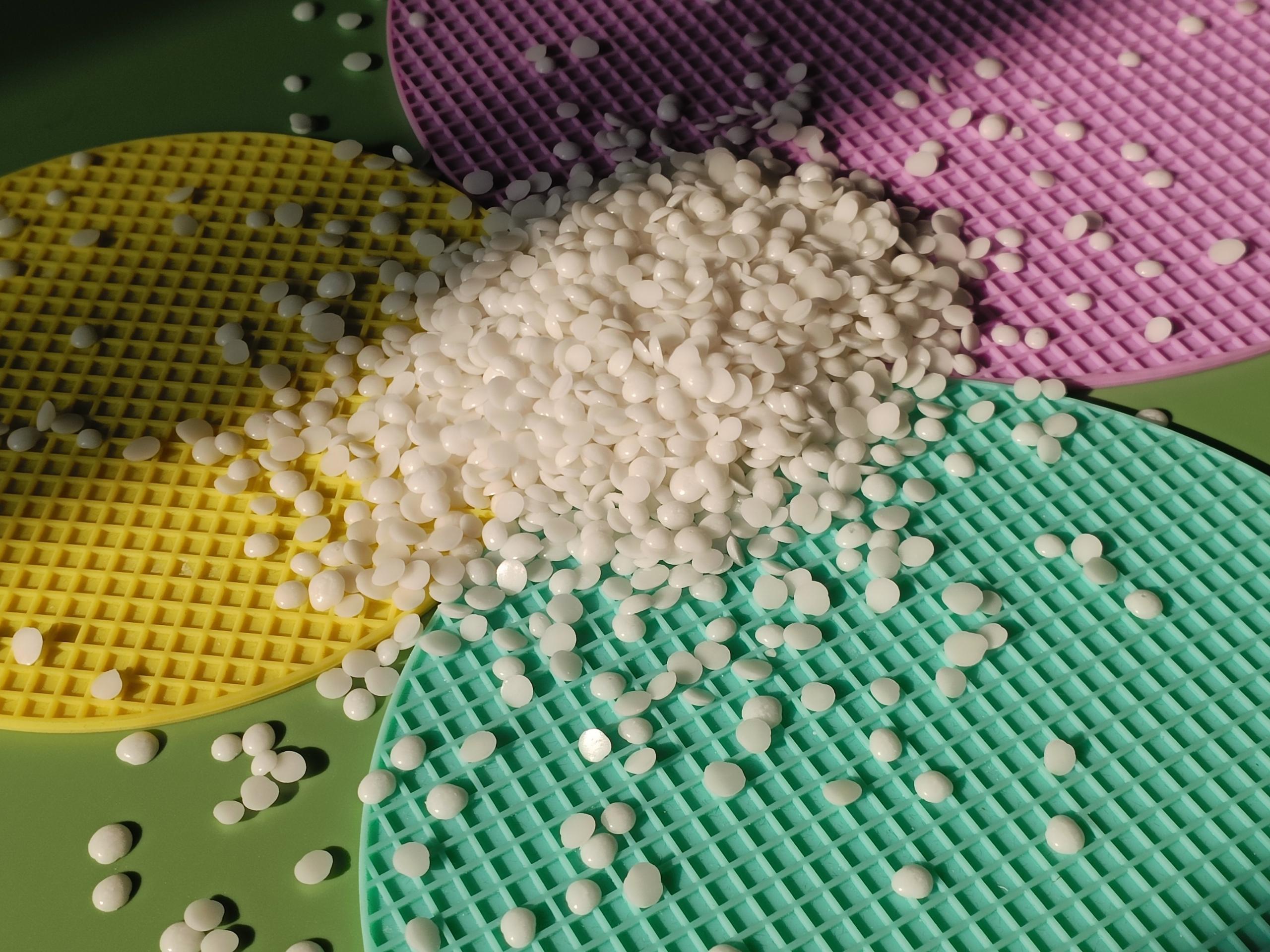
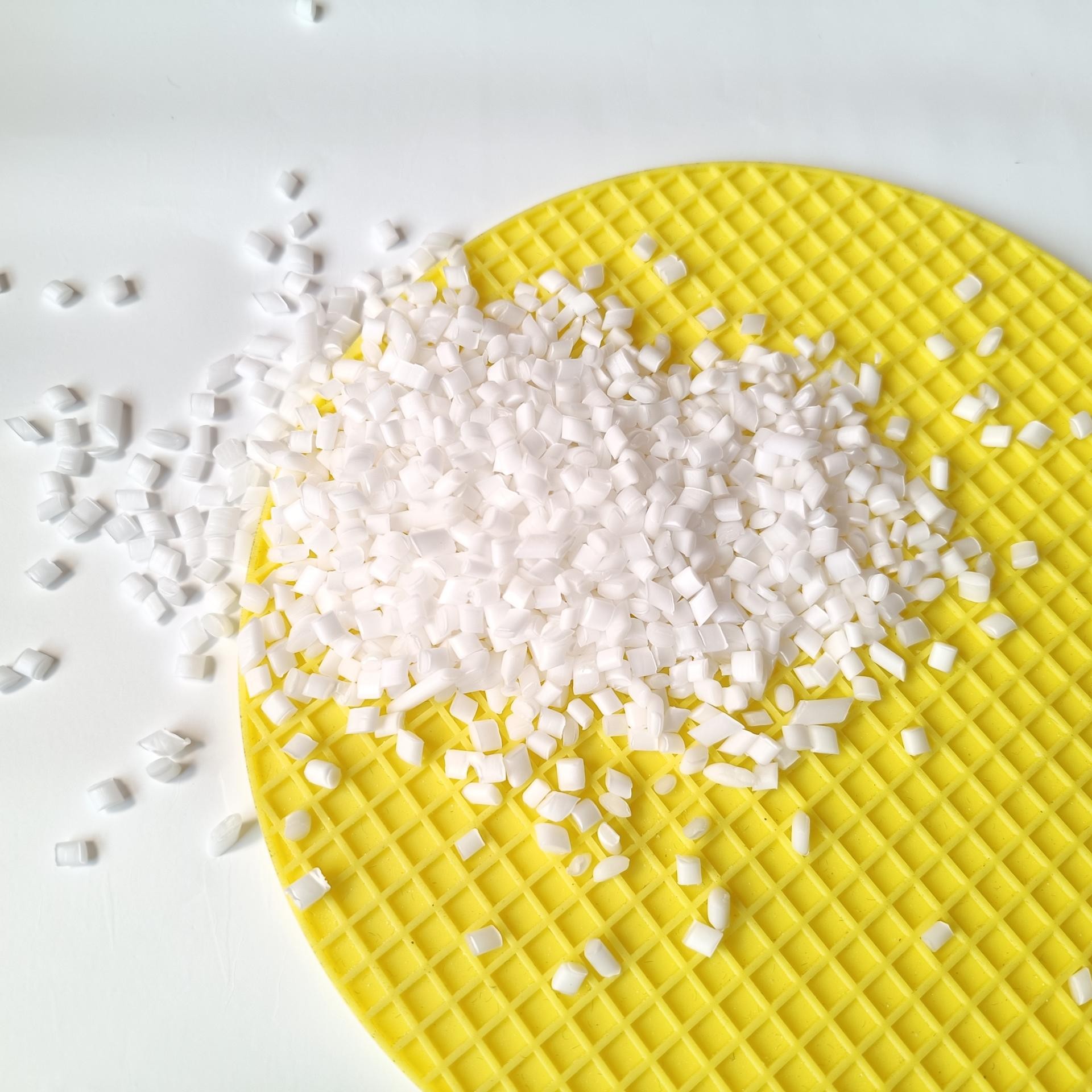
4. Anti-Scratch Coatings
While not an additive per se, applying anti-scratch coatings to TPE products is a common approach to improving their surface durability. These coatings can be formulated with various materials, including silanes, polyurethanes, or UV-cured resins, to provide a hard, protective layer.
- Function: Provides a hard, durable surface layer that protects against scratches and marring.
- Benefits: Coatings can be tailored to specific applications and provide long-lasting protection.
5. Fluoropolymers
Fluoropolymer-based additives are known for their excellent chemical resistance and low surface energy, which reduces friction and enhances the scratch resistance of TPEs.
- Function: Provides a low-friction surface that is resistant to chemicals and wear.
- Benefits: Offers excellent scratch resistance and longevity, making them ideal for high-performance applications.
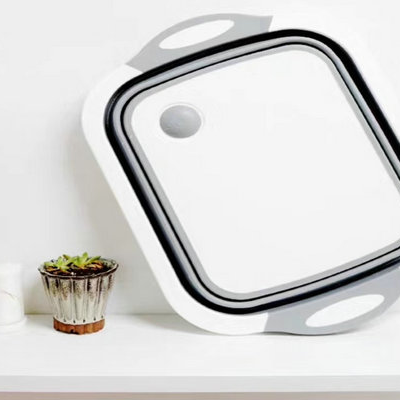
Factors Influencing the Effectiveness of Additives
The effectiveness of these additives in improving scratch and mar resistance depends on several factors:
- Concentration: The amount of additive used can significantly impact the final properties of the TPE. Optimal concentrations must be determined to balance improved resistance with other material characteristics.
- Compatibility: The additive must be compatible with the TPE matrix to ensure even distribution and effective performance.
- Processing Conditions: The processing conditions, such as temperature and shear rate during compounding, can affect the dispersion of additives and their ultimate effectiveness.
To learn more about how Thermoplastic Silicone-based elastomer modifiers can enhance TPE materials, elevating your final product's surface aesthetics and improving scratch and mar resistance, please contact SILIKE today. Experience the benefits of a dry, silky touch with no blooming, even after long-term use.
Tel: +86-28-83625089 or via email: amy.wang@silike.cn. website:www.si-tpv.com
Related News

