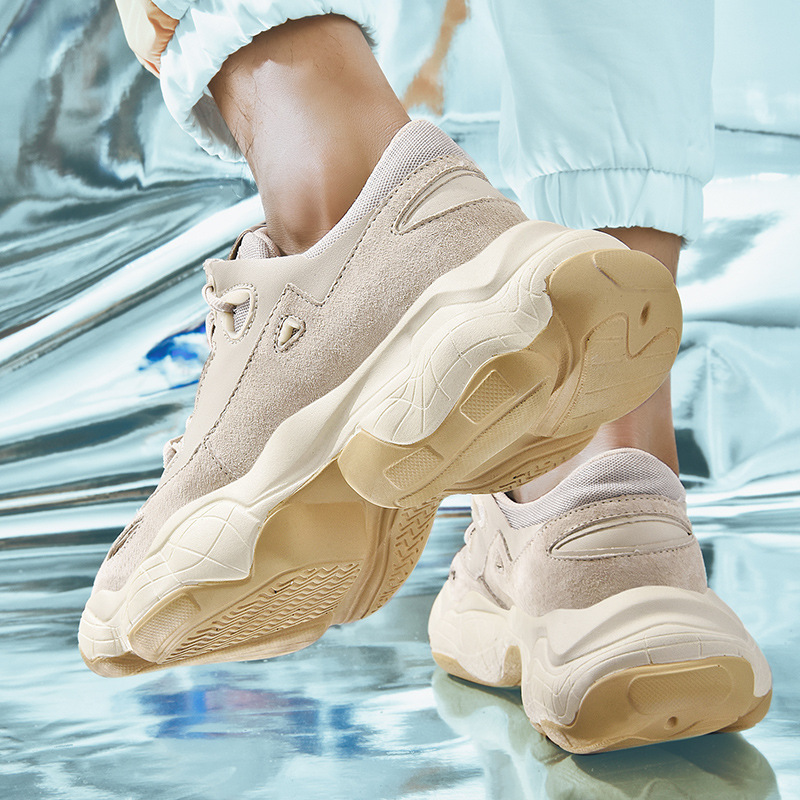
In recent years, the global footwear market has witnessed saturation, intensifying competition among mid- to high-end brands. The continuous influx of new concepts and technologies in footwear has driven a substantial demand for foaming materials in the shoemaking industry. High-performance polymer foam materials have become the cornerstone of numerous terminal brand product solutions, particularly in the sports footwear sector.
A standard pair of sports shoes comprises three main parts: the upper, midsole, and outsole.
The midsole is pivotal in delivering cushioning, rebound, and impact force absorption during sports. It ensures protection and a comfortable feel, making it the soul of athletic shoes. The material and foaming technology of the midsole differentiates the core technologies of various major brands.
EVA—The Earliest Used Foam Material for Shoes:
Ethylene-vinyl acetate copolymer (EVA) is the earliest foam material used in midsoles. Pure EVA foam typically boasts a rebound of 40-45%, surpassing materials like PVC and rubber in resilience, coupled with attributes such as lightweight and ease of processing.
In the footwear field, EVA's chemical foaming processes generally include three types: traditional flat large foaming, in-mold small foaming, and injection cross-linking foaming.
Presently, injection cross-linking foaming has become the mainstream process in shoe material processing.
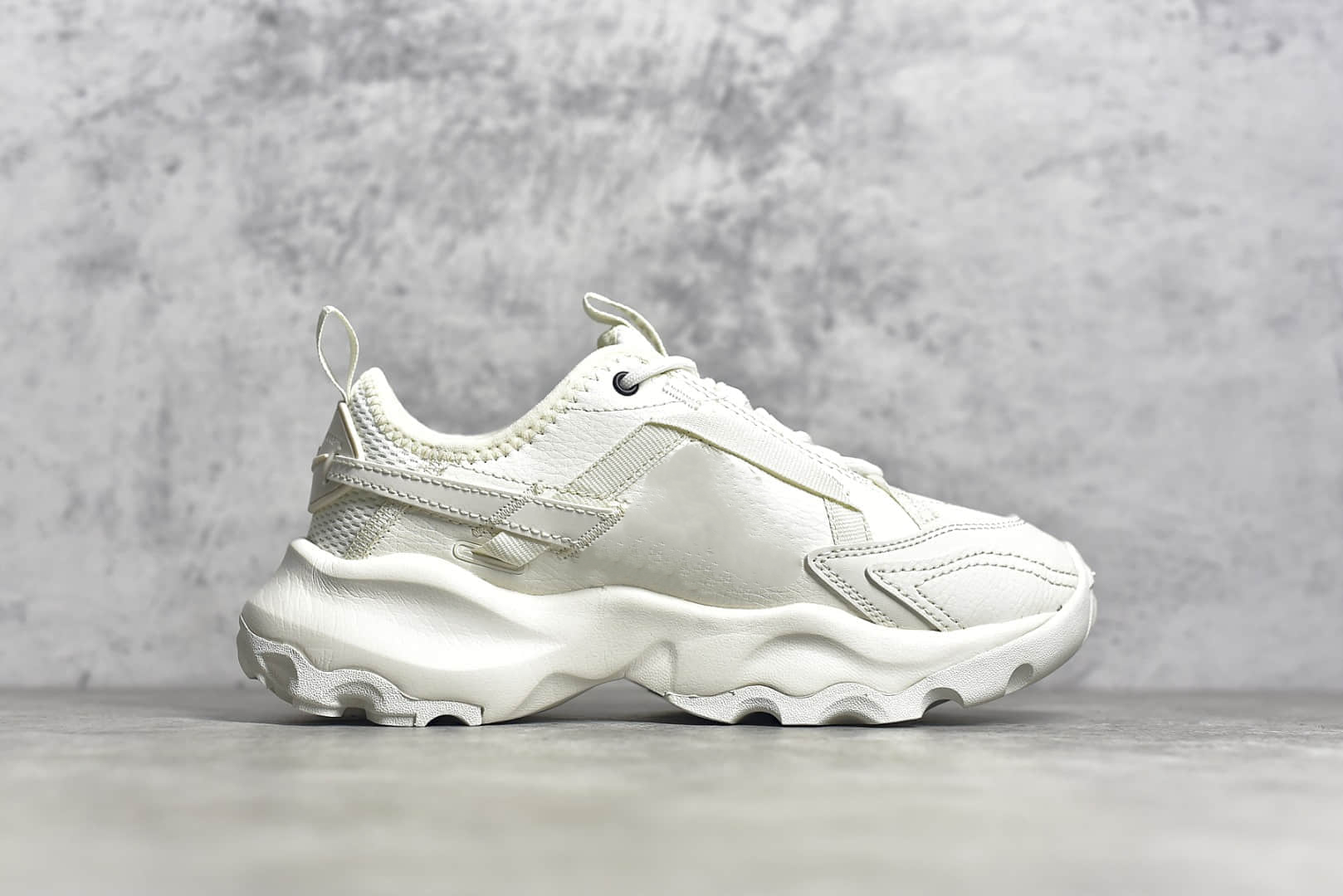
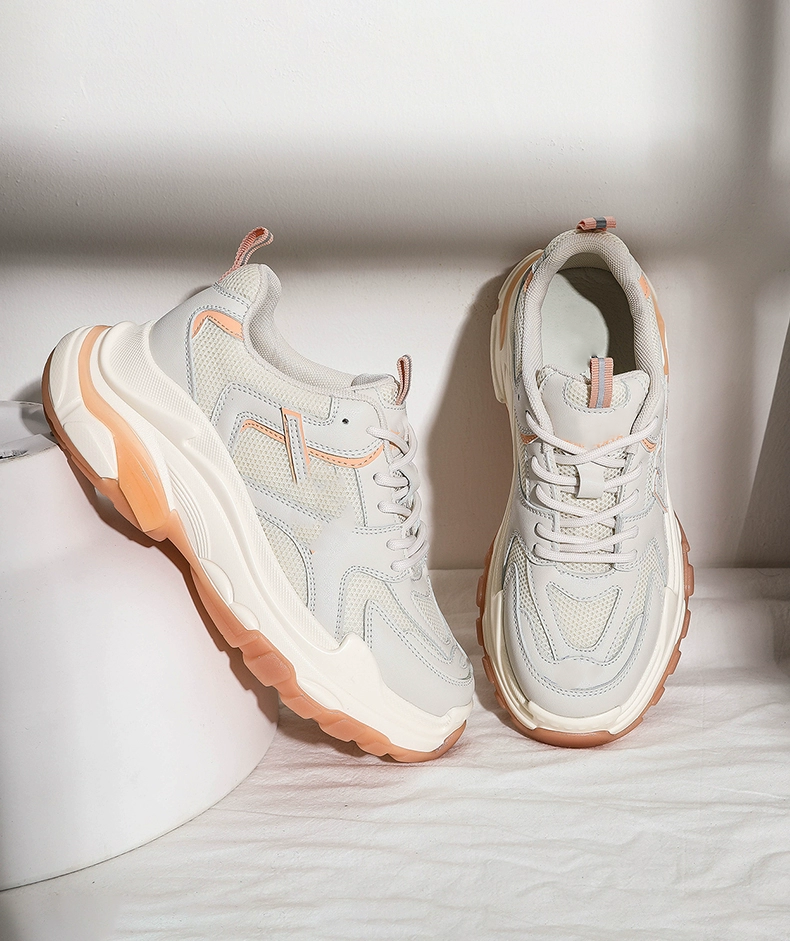
EVA Foam Challenges:
A common problem with these traditional EVA foams is their limited elasticity, which affects their ability to provide optimal cushioning and support, especially in applications such as sports shoes. Another common challenge is the occurrence of compression set and thermal shrinkage over time, affecting durability. Moreover, In applications where slip resistance and abrasion resistance are critical, traditional EVA foam may fall short of meeting the required standards.
To further enhance the physical properties of EVA foam products, manufacturers frequently introduce elastic materials like EPDM, POE, OBCs, and TPE such as SEBS into EVA raw materials. The incorporation of EPDM for rubber properties, POE for high elasticity, OBCs for soft crystallinity, TPE for flexibility, etc., aims to achieve modification goals. For instance, by adding POE elastomers, the rebound resilience of products can often be increased to 50-55% or even higher.
Innovation EVA Foam: Si-TPV Modifier for Higher Quality and Enhanced Performance
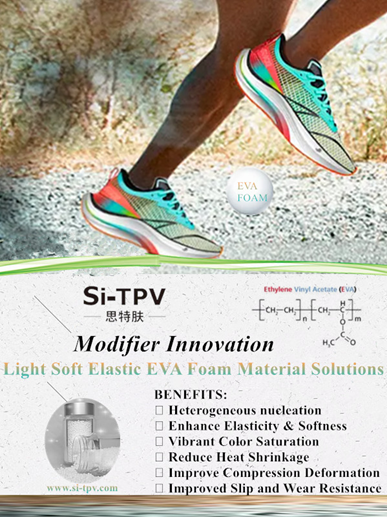
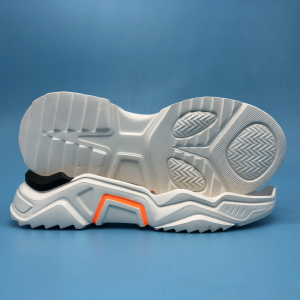
SILIKE Si-TPV presents an alternative approach in EVA, not only addresses performance issues but also aligns with eco-friendly initiatives. Its innovative composition and production process contribute to ensuring that products maintain their integrity and functionality over extended periods, making them more reliable and durable. ensuring higher finished product rates.
Si-TPV ( vulcanizate thermoplastic silicone-based elastomer) is a 100% recyclable elastomer material, Compared to OBC and POE, it notably reduces the compression set and heat shrinkage rate of EVA foam materials. More highlights improved elasticity, softness, anti-slip, and abrasion resistance, reducing DIN wear from 580 mm3 to 179 mm3.
In addition, Si-TPV enhances the color saturation of EVA foam materials. This breakthrough allows manufacturers to produce visually appealing products without compromising on performance.
This Si-TPV as an innovation modifier for EVA foam benefits the production of comfort and durable EVA foaming-related products such as midsoles, sanitary items, sports leisure products, floors, yoga mats, and more.
Discover the Future of EVA Foam with SILIKE Si-TPV! Elevate your products to new heights of performance and quality. Unleash the potential of our progressive Si-TPV modifier for unparalleled possibilities in your EVA foam applications.
Contact us today to embark on a journey of innovation and redefine what's possible with EVA foam!
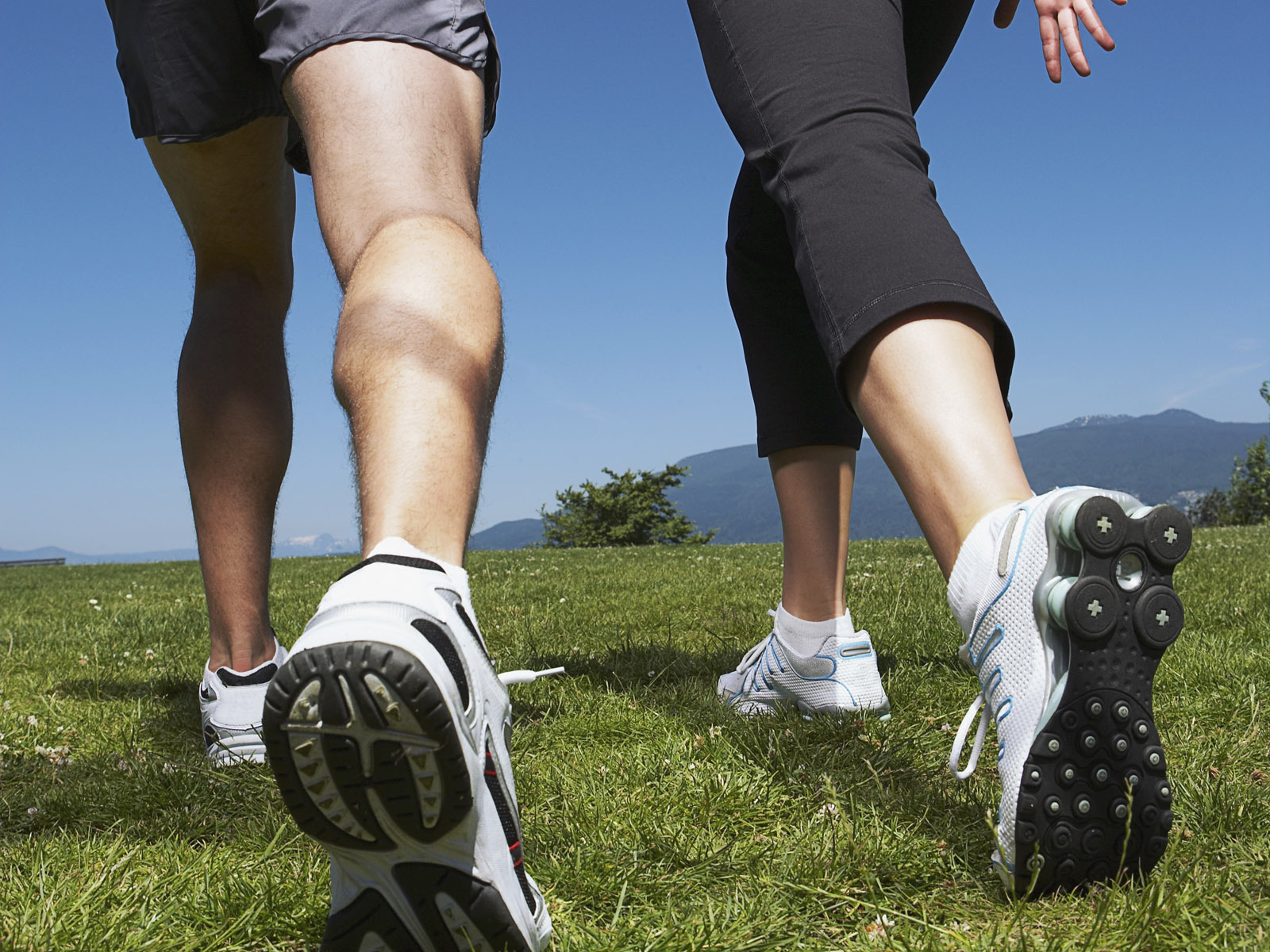
Related News

