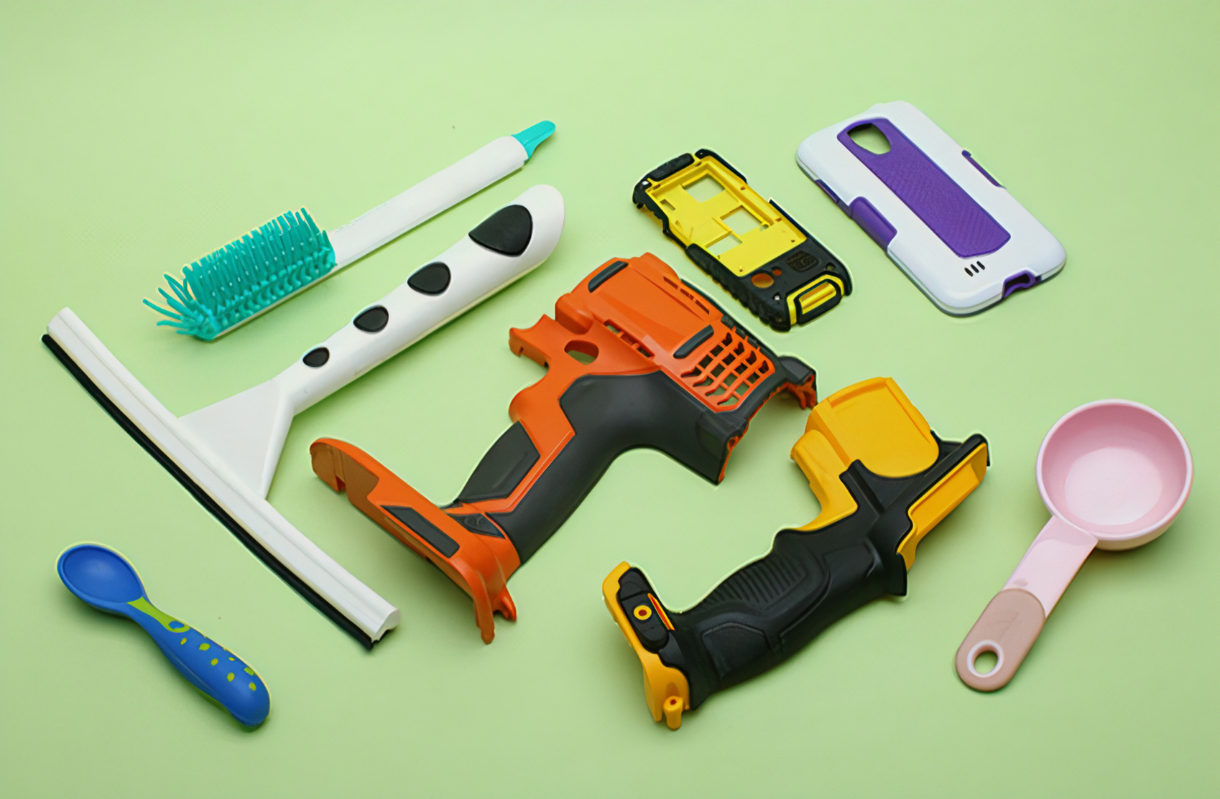
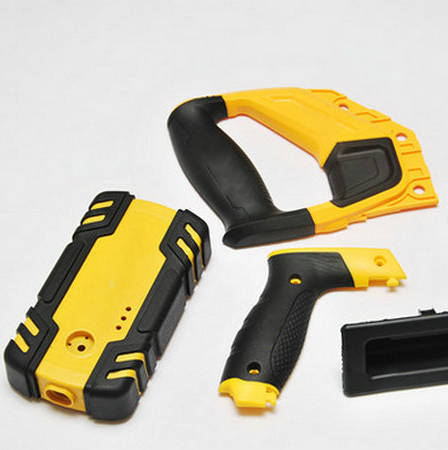
In the ever-evolving landscape of manufacturing and product design, engineers and designers are constantly exploring innovative techniques to improve the functionality, durability, and aesthetics of their products. Overmolding is one such technique that has gained prominence for its ability to combine different materials into a single, integrated product. This process not only enhances the product's performance but also opens up new possibilities for design and customization.
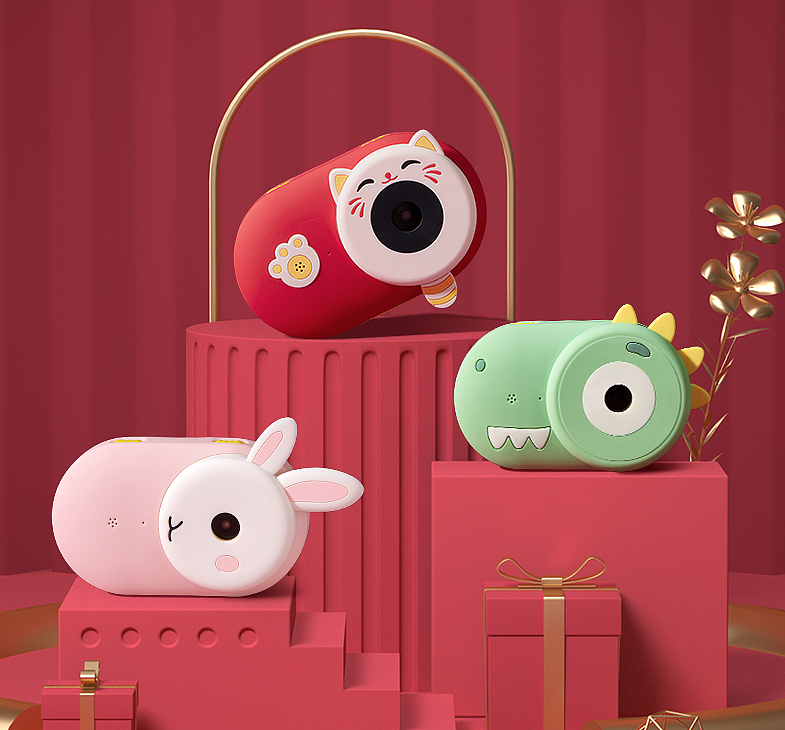
What is Overmolding?
Overmolding, also known as two-shot molding or multi-material molding, is a manufacturing process where two or more materials are molded together to create a single, integrated product. This technique involves injecting one material over another to achieve a product with improved properties, such as enhanced grip, increased durability, and added aesthetic appeal.
The process typically involves two steps. First, a base material, often a rigid plastic, is molded into a specific shape or structure. In the second step, a second material, which is usually a softer and more flexible material, is injected over the first to create the final product. The two materials chemically bond during the molding process, creating a seamless integration.
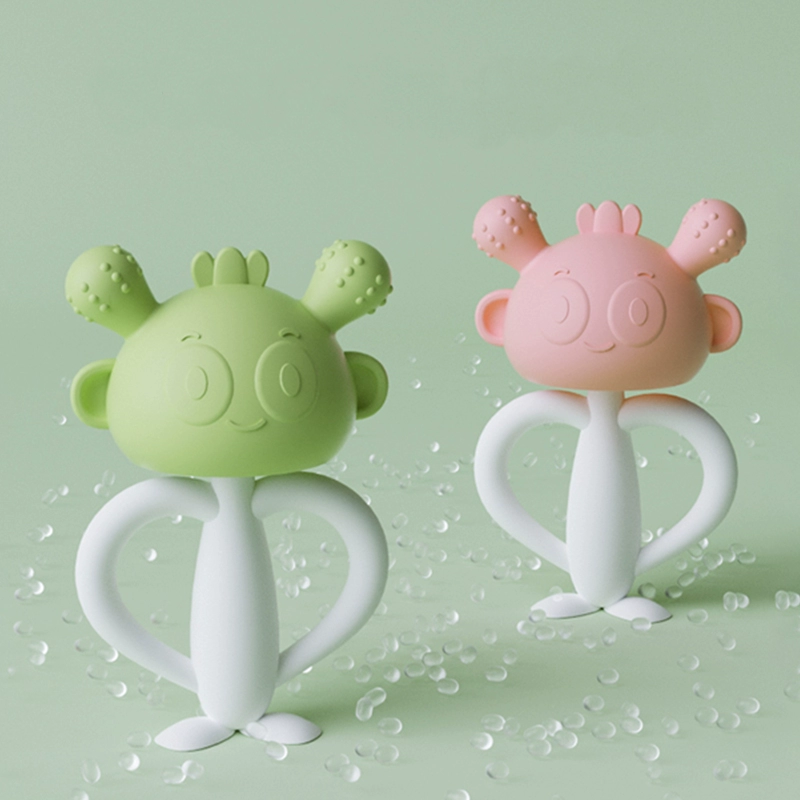
Materials Used in Overmolding
Overmolding allows for the combination of a wide range of materials, each with its unique properties. Common combinations include:
Thermoplastic Over Thermoplastic: This involves using two different thermoplastic materials. For example, a hard plastic substrate may be overmolded with a softer, rubber-like material to improve grip and ergonomics.
Thermoplastic Over Metal: Overmolding can also be applied to metal components. This is often seen in tools and equipment where a plastic overmold is added to metal handles for improved comfort and insulation.
Thermoplastic Over Elastomer: Elastomers, which are rubber-like materials, are frequently used in overmolding. This combination provides products with a soft-touch feel and excellent shock absorption properties.
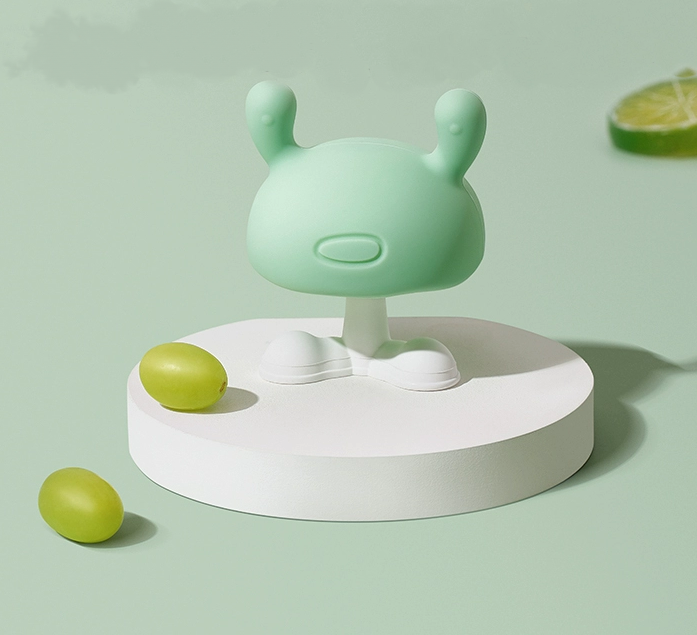
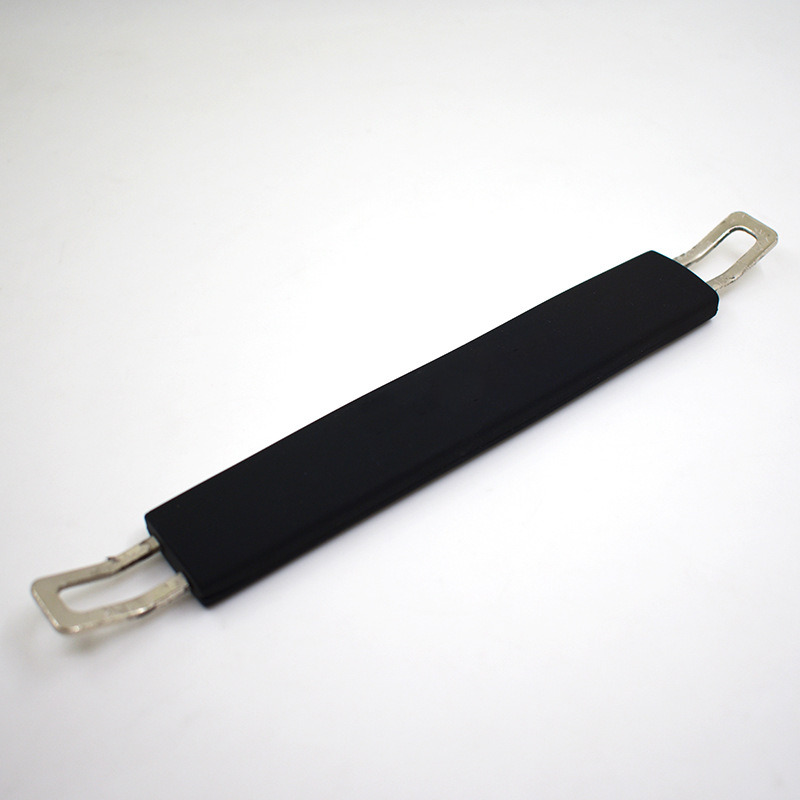
Advantages of Overmolding:
Enhanced Functionality: Overmolding allows for the combination of materials with complementary properties. This can lead to products that are not only more durable but also more comfortable to use.
Improved Aesthetics: The ability to use different colors and textures in the overmolding process enables designers to create products with enhanced visual appeal.
Cost Efficiency: While the initial setup costs for overmolding may be higher, the process often results in a more cost-effective final product. This is because it eliminates the need for secondary assembly processes.
Reduced Waste: Overmolding can reduce material waste as it allows for the precise application of materials only where needed.
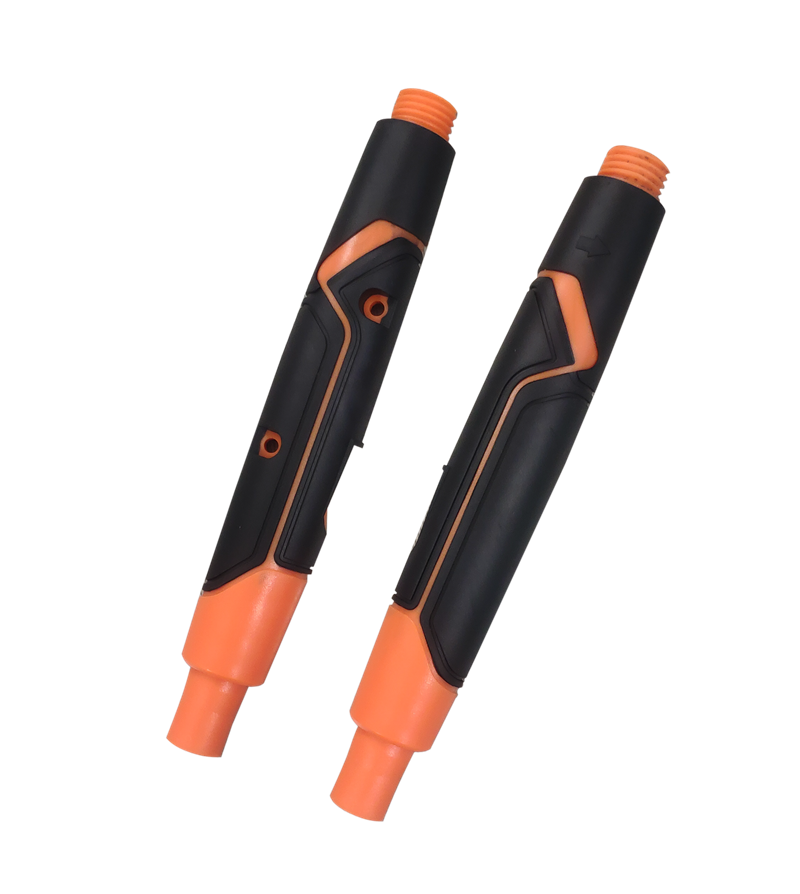
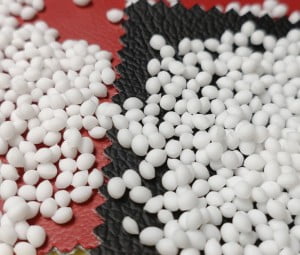
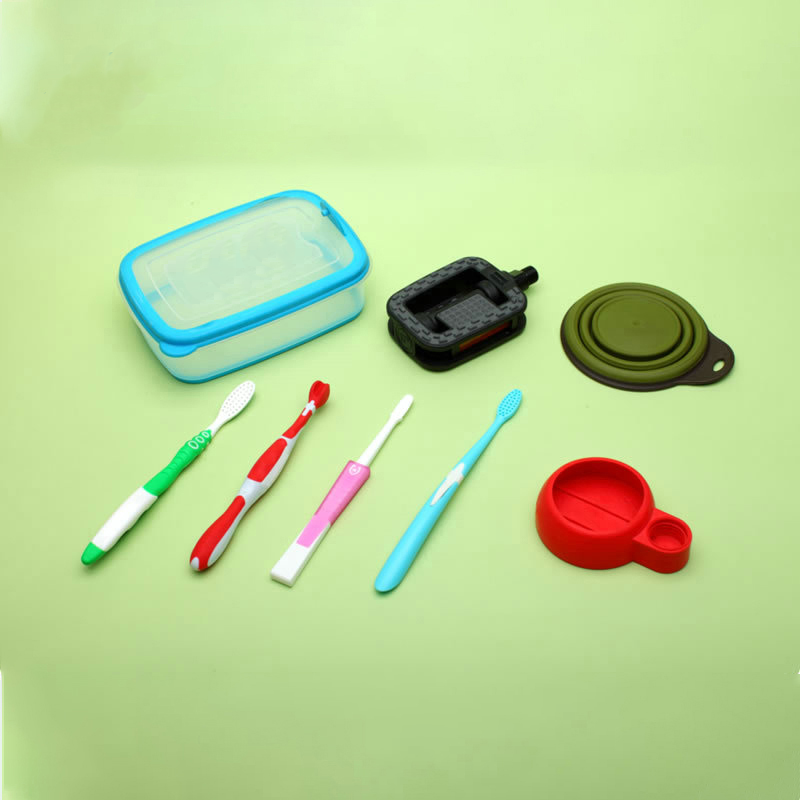
Applications of Overmolding:
Consumer Electronics: Overmolding is commonly used in the production of electronic devices, providing a comfortable grip, durability, and a sleek design.
Automotive Industry: Overmolding is employed in automotive components, such as steering wheels, handles, and grips, to enhance both functionality and aesthetics.
Medical Devices: In the medical field, overmolding is utilized to create ergonomic and biocompatible products, ensuring comfort and safety for patients and healthcare professionals.
Tools and Equipment: Overmolding is applied to tool handles and equipment grips to improve user comfort and control.
Unlocking Innovation: Si-TPV redefines soft-touch overmolding across diverse industries.
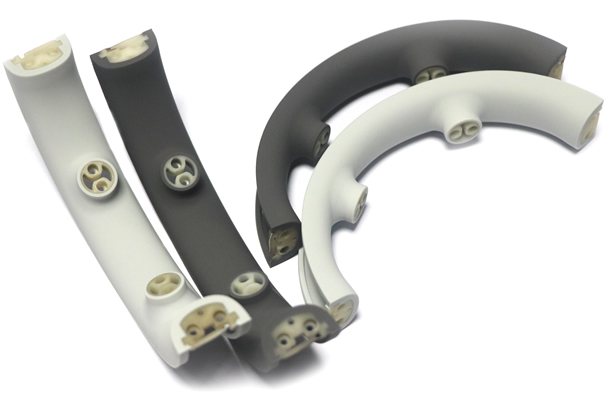
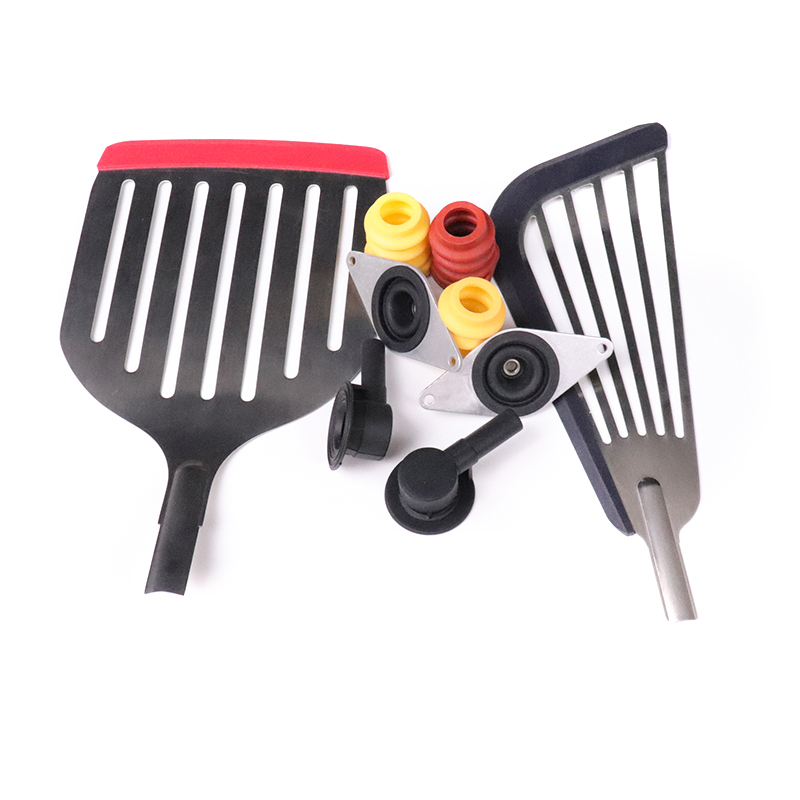
One key aspect shaping the future of soft-touch overmolding is the development of materials with enhanced compatibility. Through specialized technologies, like SILIKE introduces a groundbreaking solution that transcends conventional boundaries – the Si-TPV thermoplastic elastomer. The material's distinctive composition combines the robust characteristics of thermoplastic elastomers with the desirable traits of silicone, including softness, a silky touch, and resistance to UV light and chemicals. Si-TPV exemplifies sustainability by being recyclable and reusable in traditional manufacturing processes. This not only enhances the eco-friendliness of the material but also contributes to more sustainable production practices.
One of the remarkable features of Si-TPV give an improved silicone rubber-like feel to finished over-molded parts. while excellent bonding capability. It seamlessly adheres to a variety of substrates, including TPE and similar polar materials like PP, PA, PE, and PS. This versatility opens up a world of possibilities for product designers and manufacturers.
SILIKE Si-TPV serves sporting &leisure equipment, personal care, power &hand tools, lawn and garden tools, toys, eyewear, cosmetic packaging, healthcare devices, smart wearable devices, portable electronics, hand-held electronics, household, other appliances markets, with low compression set and long-lasting silky feel, and stain resistance, these grades meet application-specific needs for aesthetics, safety, antimicrobial and grippy technologies, chemical resistance, and more.
Discover the endless opportunities for innovation and enhanced user experience with our advanced soft-touch overmolding solutions. Whether you're in consumer electronics, automotive design, Medical Devices, Tools and Equipment, or any industry that values comfort and sophistication, SILIKE is your partner in material excellence.
Related News

