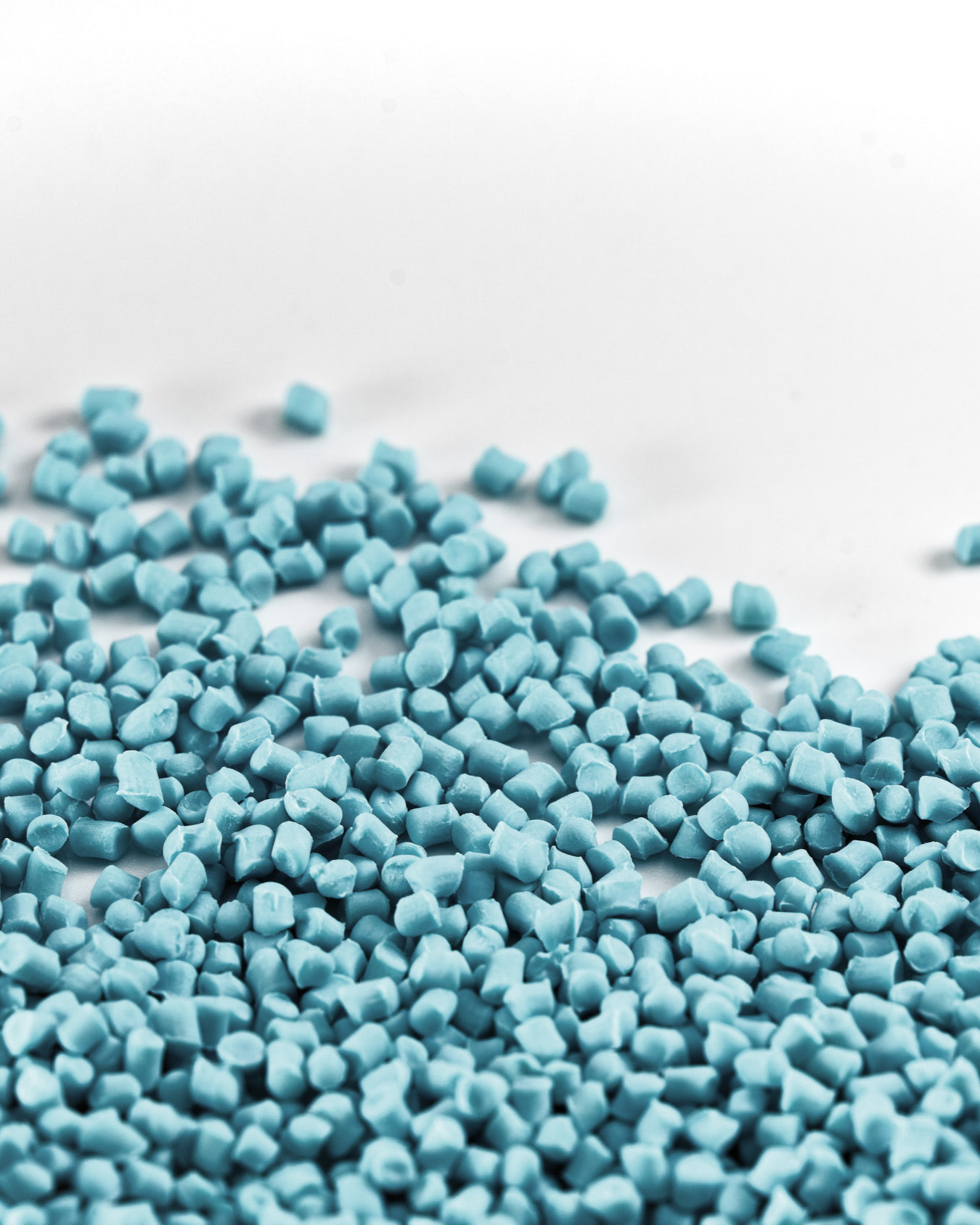
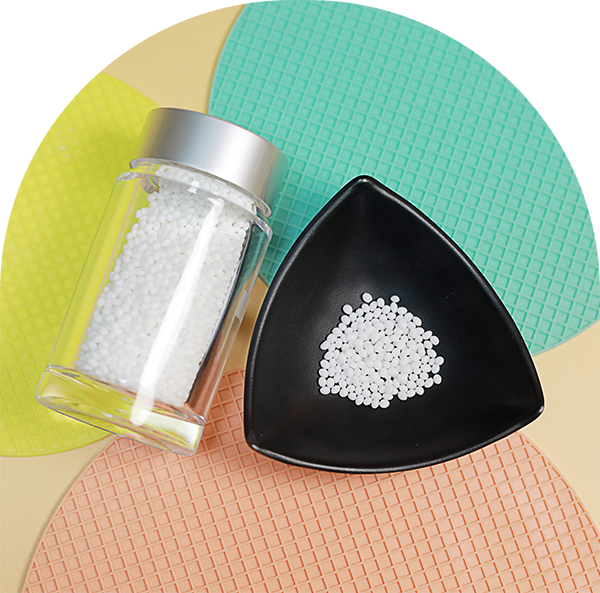
Introduction:
In the world of materials science and engineering, innovations often emerge that promise to revolutionize industries and reshape the way we approach design and manufacturing. One such innovation is the development and adoption of dynamic vulcanizate thermoplastic Silicone-based elastomer (generally shortened to Si-TPV), a versatile material that has the potential to replace traditional TPE, TPU, and silicone in various applications.
Si-TPV offers a surface with a unique silky and skin-friendly touch, excellent dirt collection resistance, better scratch resistance, does not contain plasticizer and softening oil, no bleeding / sticky risk, and no odors, which makes it an attractive alternative to TPE, TPU, and silicone in many scenarios, from consumer products to industrial applications.
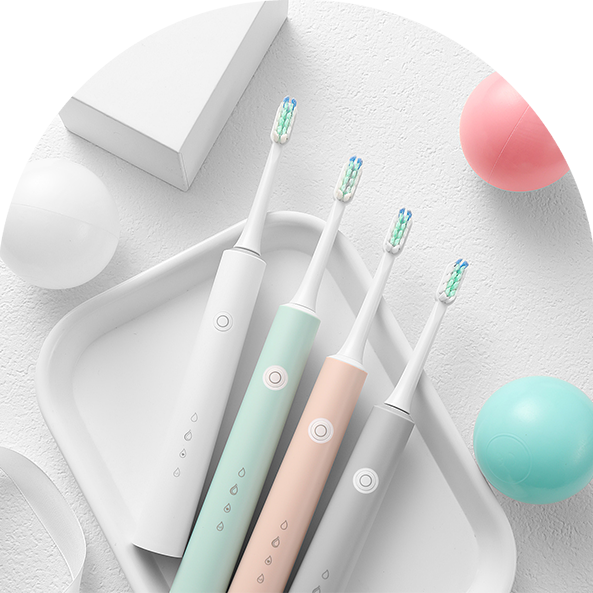
To determine when Si-TPVs can effectively replace TPE, TPU, and silicone, we need to examine their respective properties, applications, and advantages. In this article, Have a look first at Understanding Si-TPV and TPE!
A Comparative Analysis of TPE & Si-TPV
1. TPE (Thermoplastic Elastomers):
TPEs are a class of versatile materials that combine the properties of thermoplastics and elastomers.
They are known for their flexibility, resilience, and ease of processing.
TPEs include various subtypes, such as TPE-S (Styrenic), TPE-O (Olefinic), and TPE-U (Urethane), each with distinct properties.
2.Si-TPV ( dynamic vulcanizate thermoplastic Silicone-based elastomer ):
Si-TPV is a newer entrant in the elastomer market, blending the benefits of silicone rubber and thermoplastics.
It offers excellent resistance to heat, UV radiation, and chemicals, Si-TPV can be processed using standard thermoplastic methods like injection molding and extrusion.

When Can Si-TPV Alternative TPE?
1. High-Temperature Applications
One of the primary advantages of Si-TPV over most TPEs is its exceptional resistance to high temperatures. TPEs can soften or lose their elastic properties at elevated temperatures, limiting their suitability for applications where heat resistance is crucial. Si-TPV on the other hand, maintains its flexibility and integrity even at extreme temperatures, making it an ideal replacement for TPE in applications like automotive components, cookware handles, and industrial equipment subjected to heat.
2. Chemical Resistance
Si-TPV demonstrates superior resistance to chemicals, oils, and solvents compared to many TPE variants. This makes it a suitable choice for applications that require exposure to harsh chemical environments, such as seals, gaskets, and hoses in chemical processing equipment. TPEs may not provide the same level of chemical resistance in such scenarios.
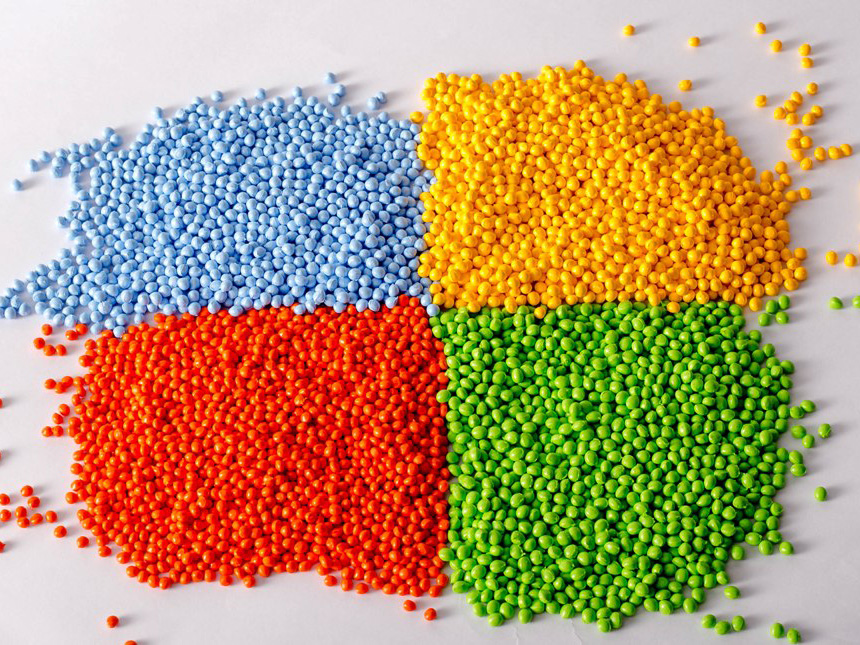
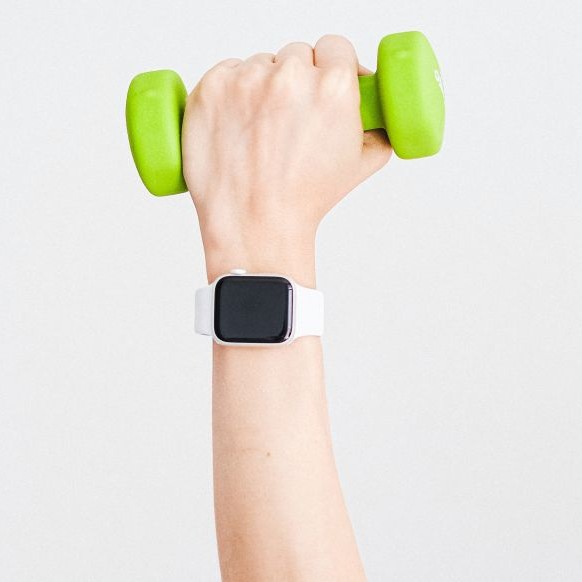
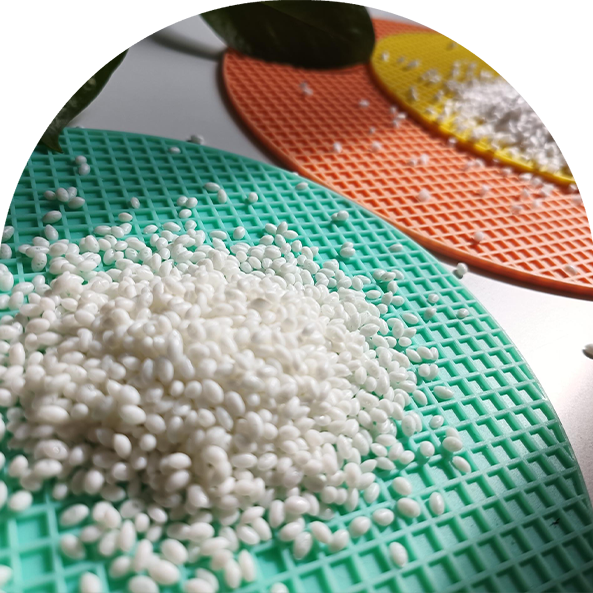
3. Durability and Weatherability
In outdoor and harsh environmental conditions, Si-TPV outperforms TPEs in terms of durability and weather ability. Si-TPV 's resistance to UV radiation and weathering makes it a reliable choice for outdoor applications, including seals and gaskets in construction, agriculture, and marine equipment. TPEs may degrade or lose their properties when exposed to prolonged sunlight and environmental factors.
4. Biocompatibility
For medical and healthcare applications, biocompatibility is essential. While some TPE formulations are biocompatible, Si-TPV offers a unique combination of biocompatibility and exceptional temperature resistance, making it a preferred choice for components like medical tubing and seals that require both properties.
5. Reprocessing and Recycling
Si-TPV 's thermoplastic nature allows for easier reprocessing and recycling compared to TPEs. This aspect aligns with sustainability goals and reduces material waste, making Si-TPV an attractive choice for manufacturers aiming to reduce their environmental footprint.
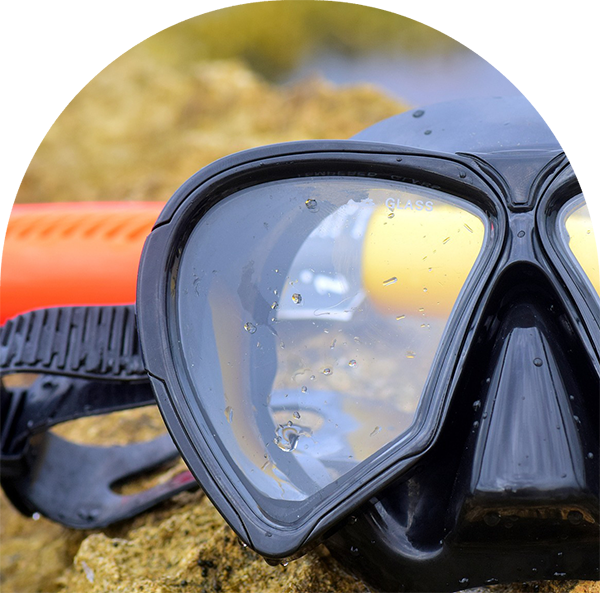
Conclusion:
It's always a good idea to research and verify the current market offerings product Si-TPV when looking for TPE!!
Although TPEs have been widely used in various applications due to their versatility. However, Si-TPV 's emergence has introduced a compelling alternative, particularly in scenarios where high-temperature resistance, chemical resistance, and durability is critical. Si-TPV 's unique combination of properties makes it a strong contender to replace TPEs in numerous industries, from automotive and industrial to healthcare and outdoor applications. As research and development in materials science continue to advance, Si-TPV 's role in replacing TPEs is likely to expand, offering manufacturers more choices to optimize their products for specific needs.
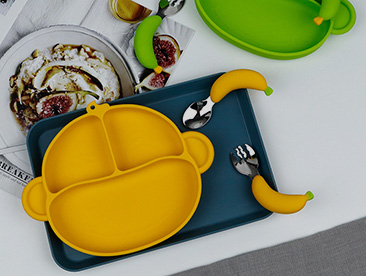
Related News

