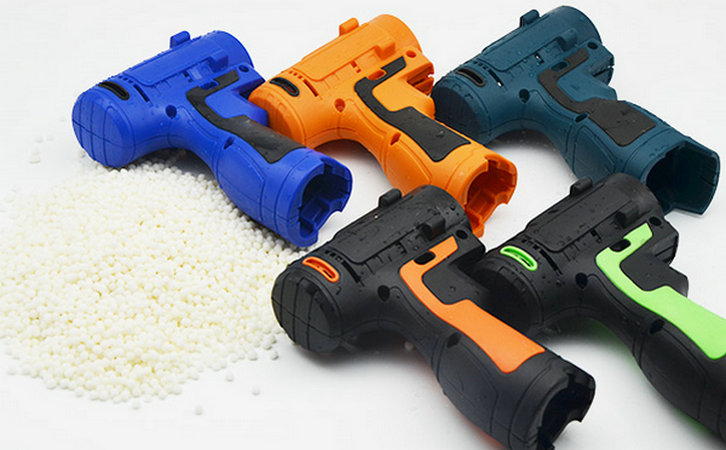
What is Nylon Overmolding?
Nylon overmolding, also known as nylon two-shot molding or insert molding, is a manufacturing process used to create parts with multiple materials. It typically involves injecting molten nylon over a pre-formed substrate, such as plastic, metal, or another material, to create a single, integrated component. This process allows for the combination of different materials with distinct properties, resulting in parts that offer enhanced functionality and performance.
Challenges in Nylon Overmolding:
1. Adhesion Issues: Achieving strong adhesion between the nylon and substrate material can be challenging, especially when the substrate has a smooth or non-porous surface, and when working with dissimilar materials. Poor adhesion can lead to delamination, part failure, and reduced durability.
2. Warping and Shrinkage: Nylon is prone to warping and shrinkage during the molding process, which can result in dimensional inaccuracies and potential defects in the final product. This issue is particularly prevalent in large or complex parts.
3. Material Compatibility: Compatibility issues may arise when overmolding nylon onto certain substrates, leading to bonding failures, or material degradation and surface defects. It is essential to carefully select compatible materials and surface treatments to ensure successful overmolding
4. Cost: Nylon overmolding can be more expensive than traditional molding processes, especially when considering material costs, tooling expenses, and production time.
Solutions to Overcome Challenges in Nylon Overmolding :
1. Surface Preparation: Proper surface preparation is essential to ensure strong adhesion between the nylon and substrate material. This may involve cleaning, priming, or roughening the substrate surface to promote bonding.Techniques such as surface roughening, chemical etching, or plasma treatment can improve bonding between the nylon and substrate.
2. Mold Design Optimization: Optimizing the mold design can help minimize warping and shrinkage issues associated with nylon. Features such as uniform wall thickness, adequate cooling channels, and draft angles can help control shrinkage and reduce internal stresses.
3. Material Selection: Choosing the right nylon grade and substrate material is critical for ensuring compatibility and achieving desired performance properties. Conducting material compatibility tests and selecting materials with similar coefficients of thermal expansion can mitigate potential issues.
4. Process Optimization: Fine-tuning the molding parameters, such as temperature, pressure, and cycle time, can optimize the overmolding process and improve part quality. Advanced molding techniques, such as gas-assisted injection molding, may also be employed to reduce warping and shrinkage.
5. Quality Control Measures: Implementing stringent quality control measures throughout the manufacturing process can help identify and address defects early on. Regular inspection of molded parts, dimensional accuracy checks, and performance testing can ensure that the final products meet the required specifications.
Unlocking Innovation: Si-TPV Empowering Manufacturers to Excel in Nylon Overmolding Challenges
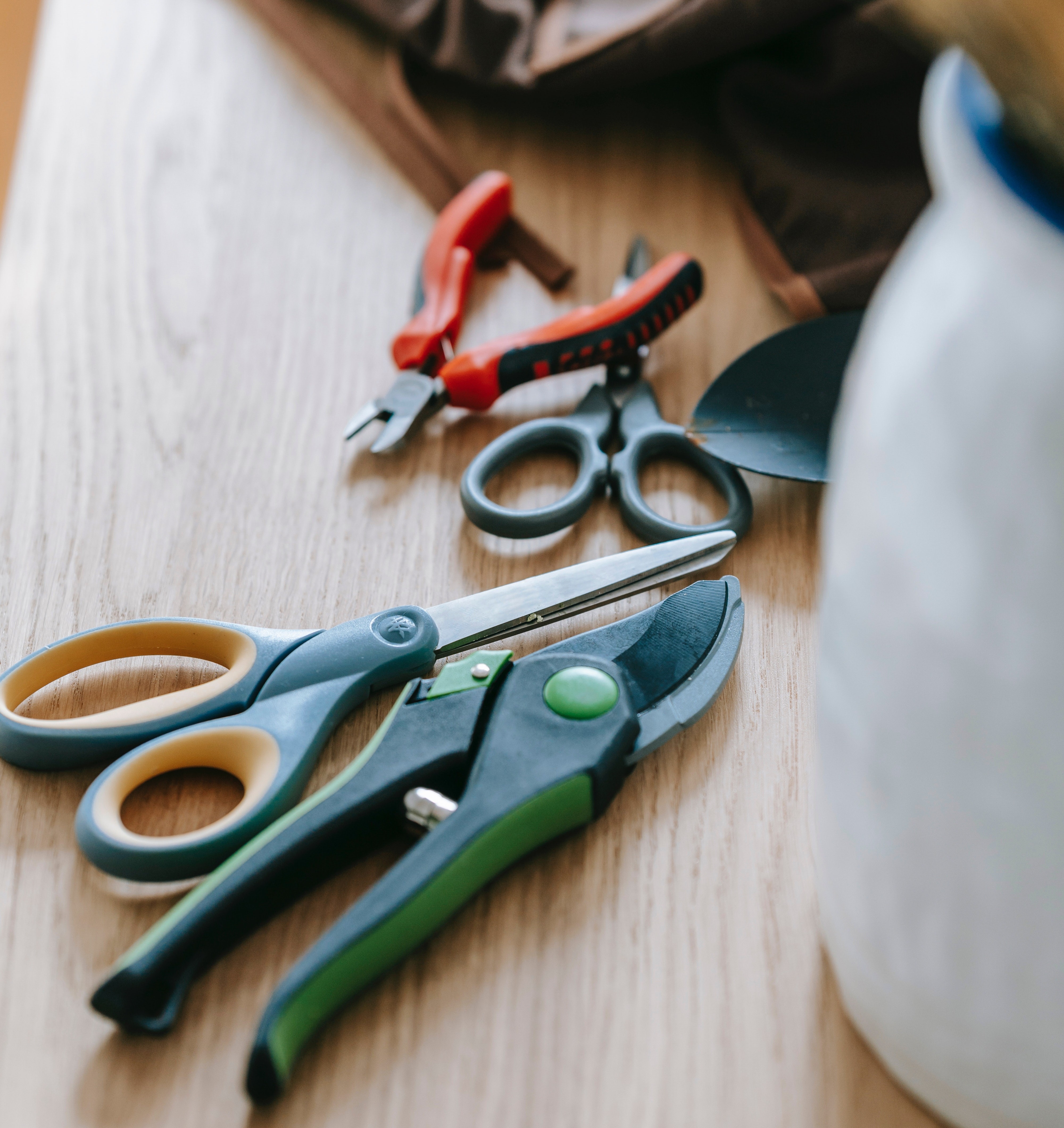
Si-TPV is a dynamic vulcanizate thermoplastic elastomer that combines the best attributes of silicone rubber and thermoplastic polymers. This innovative material offers a unique blend of softness, flexibility, and durability, making it ideal for a wide range of overmolding applications. Unlike traditional materials, Si-TPV exhibits dynamic vulcanization, allowing for superior mechanical properties and excellent adhesion to nylon substrates.
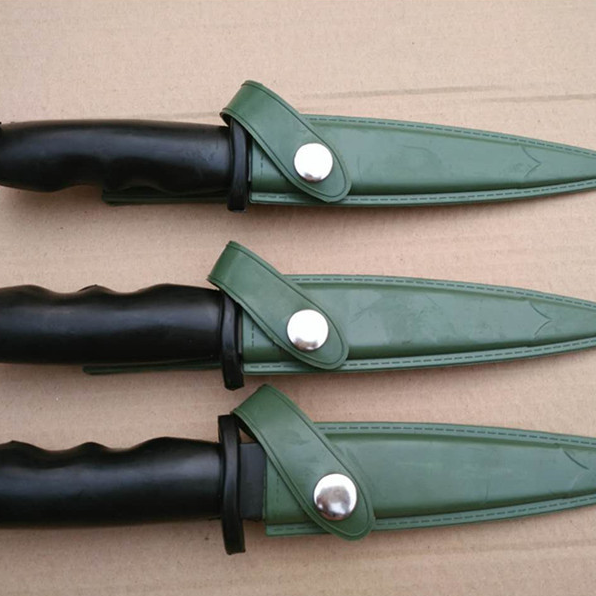
Key Advantages of Si-TPV for Nylon Overmolding:
Unmatched Softness: Si-TPV provides a soft and cushion-like feel to overmolded parts, enhancing user comfort and ergonomics. Its superior flexibility allows for the creation of complex shapes and contours, enabling designers to unleash their creativity.
Exceptional Adhesion: Si-TPV exhibits outstanding adhesion to nylon substrates, ensuring strong bonding and durability in overmolded parts. This eliminates the risk of delamination or separation, even in demanding applications.
Enhanced Durability: Si-TPV offers excellent resistance to wear, tear, and environmental factors, ensuring long-term performance and reliability in harsh conditions.
Versatility: Si-TPV is compatible with a wide range of nylon grades and processing techniques, making it suitable for various overmolding applications across industries.
Aesthetically Pleasing: Si-TPV enhances the visual appeal of overmolded parts with its smooth surface finish and vibrant colors. Its ability to retain textures and details adds to the overall aesthetics of the final product.
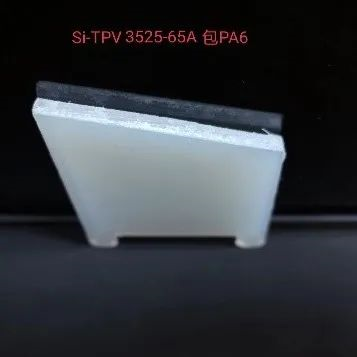
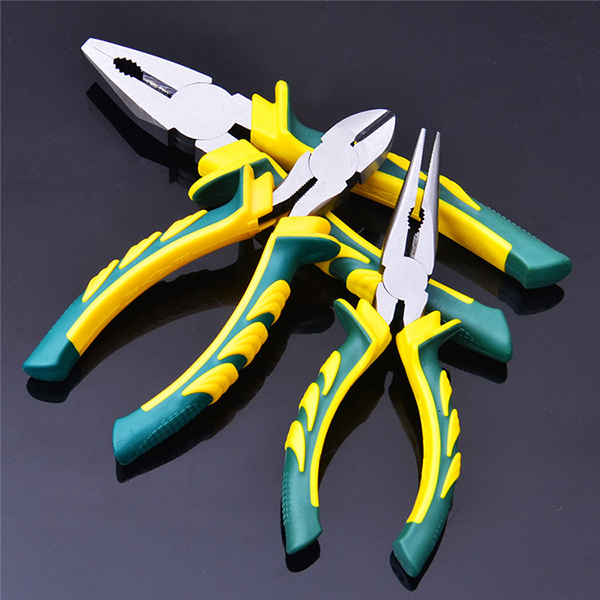
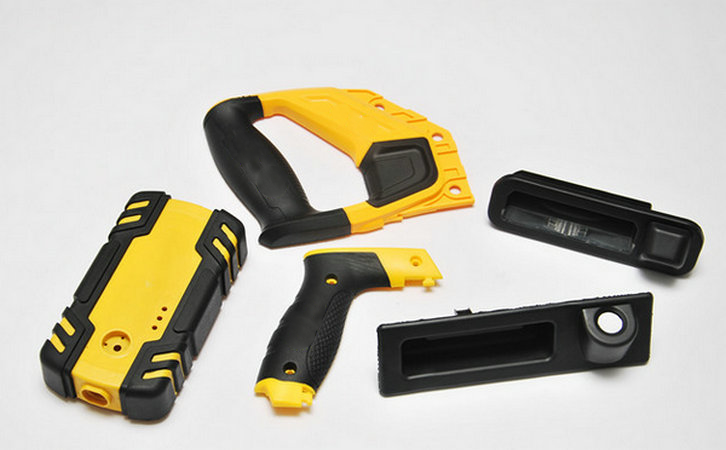
Applications of Si-TPV in Nylon Overmolding:
Si-TPV finds applications in diverse industries, including automotive, electronics, consumer goods, medical devices, and more. Some common applications include:
Automotive interior components such as soft-touch surfaces, armrests, and handles
Consumer electronics accessories like phone cases, headphone covers, and remote controls
Medical device components requiring soft and biocompatible materials
Sporting goods and equipment with ergonomic grips and cushioning
Conclusion: Si-TPV unlocks new possibilities for designers and manufacturers seeking to create innovative and high-quality overmolded products. Whether you're looking to enhance user comfort, improve product aesthetics, address adhesion Issues, tackle warping and Shrinkage, or optimize manufacturing processes, Si-TPV is the ideal choice for your nylon overmolding needs.
Don't Let Challenges Hold You Back! Embrace the power of Si-TPV and unlock new opportunities for success in nylon overmolding. Contact SILIKE now to learn more about elevating your nylon overmolding process to new heights of performance and efficiency.
Tel: +86-28-83625089 or +86-15108280799
Email: amy.wang@silike.cn
Website: www.si-tpv.com
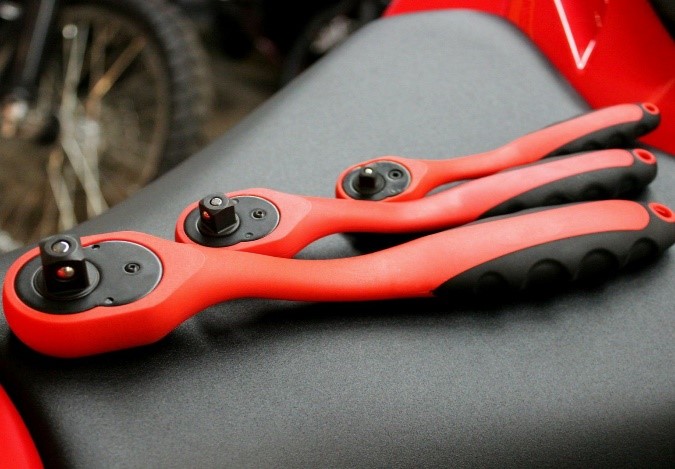
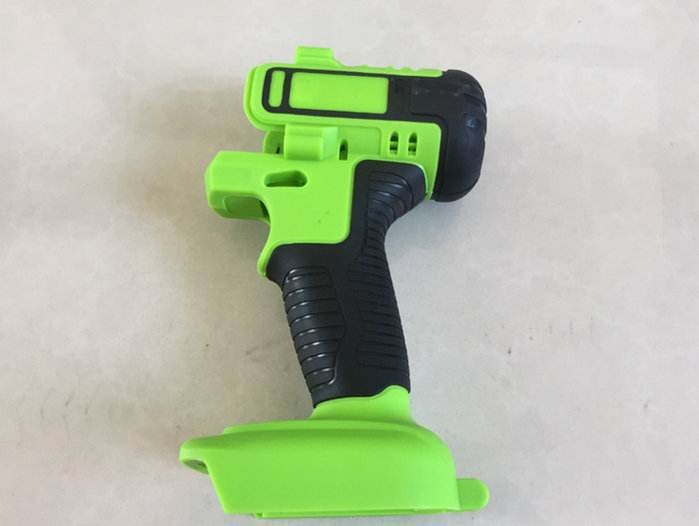
Related News

